从2016年3月至2018年3月,配天机器人打造了一条无源滤波器自动化智能柔性装配生产线,该产线覆盖了滤波器装配全工序,实现了贴标、扫码、压装、螺钉锁付、锡焊、检测以及除尘等所有工艺的自动化。
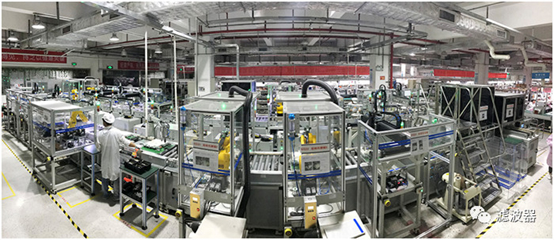
全球首条腔体滤波器自动化装配线
该生产线是目前行业内滤波器装配最完备的产线,首次实现了滤波器装配全工艺自动化,并且考虑滤波器本身外形尺寸公差较大,整线工位实现了全视觉定位,大大提高了装配精度,并简化了工装夹具的设计要求;整线调试方面,装配位置采用离线编程,免去了示教工作量,大大缩短了换产时间,提高了整线利用率。
全球首条无源腔体滤波器自动化智能柔性装配线已经投入量产,该自动化线主要用于装配无源腔体滤波器。无源腔体滤波器内部结构主体为滤波器腔体,其他需装配的零件有:连接器、抽头线、低通、谐振杆、飞杆、电感、波长线、PCB板、硬连接等。随着各装配工位的不断优化与模块化提取,该产线可扩展至其他3C装配行业。
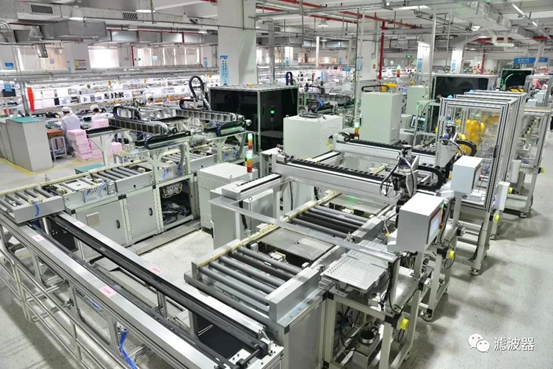
为突破装配工艺复杂、装配精度要求高、产品种类多样、换产频繁等难点,配天机器人在该产线上展现了三大核心技术:
第一,采用配天机器人本体及控制系统:重复定位精度及绝对定位精度高,可靠性强;
第二,采用视觉定位:每个自动装配工位都配有配天视觉系统,采用视觉定位,既大大提高了装配精度,又降低了对滤波器腔体上线后的定位精度要求,并且做到了先检测后装配,有效避免了误装;
第三,采用模块化设计:每个工位设计为单独模块,整条产线可根据具体工艺要求进行柔性化调整,并且每个模块都配有单独的控制系统,可脱离整线作为单机设备进行运转。
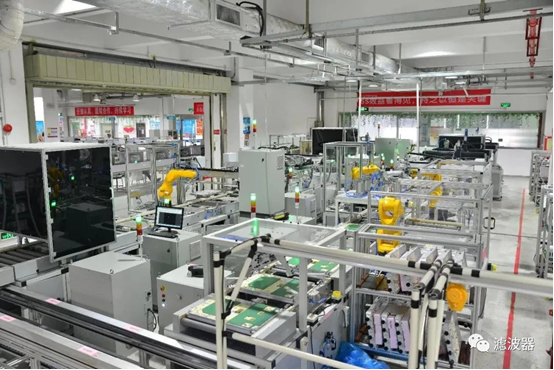
无源腔体滤波器自动化装配线整线有58个工位,包括21个自动工位,3个半自动工位,2个预留工位,2个循环流转工位,30个缓存工位;采用20套工业机器人及19套视觉系统;覆盖滤波器装配所有工艺,包括:贴标、扫码、压装、螺钉锁付、锡焊、检测以及除尘。
自该生产线投入量产后,由原35人减少至20人,节省人工42.8%;产线节拍80~90s,提高产能后由原350件/班提高至450件/班;提高产品合格率,由原95%提高至99%。
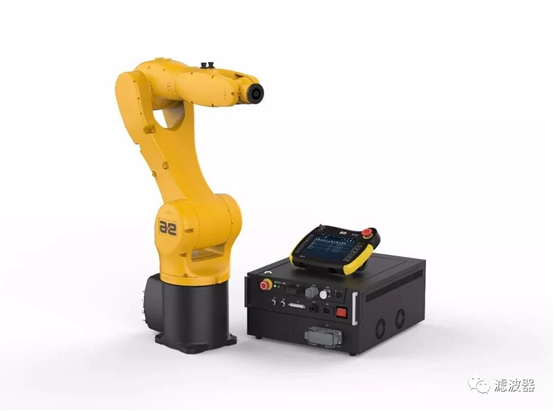
该生产线各装配工位重复定位精度为±0.02mm,产能600-800件/天;产品合格率99%;整线换产时间为30分钟。
此外,还实现了自动化检测,对于不良品实现了线上返修,有效防止了不良品的产出,大大降低了调试中才发现问题后的返修成本,最终有效降低了产品装配成本。
产线工位
包含15个自动及半自动工位,具体如下:
1)安装7/16连接器
2)气密性检测
3)压装硬连接
4)压装低通
5)压装飞杆
6)电感焊接
7)打PCB板螺钉
8)安装谐振杆
9)贴标扫码
10)半自动压装
11)腔体内焊接
12)安装定位销
13)负压除尘
14)腔体内匹配检测
15)高度位置度检测。
部分主要工位详情(附现场图)
■压装硬连接:
采用四轴直角坐标机器人安装硬连接,并兼容螺钉锁付及过盈压装两种固定方式。
末端集成有压装气缸和电批,可适应硬连接的压装和螺钉锁付两种固定方式;末端手抓和料盘可以根据不同产品进行更换,适应广泛,安装效率高。
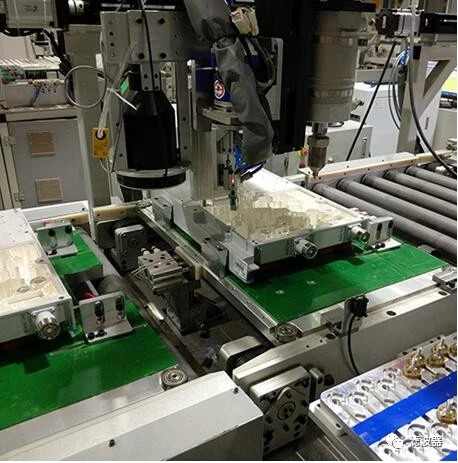
工艺简介:视觉标定滤波器工件坐标系;机器人驱动夹爪在料盘取料;机器人装配并自动供螺钉进行锁付或气缸压装。
■电感焊接
双机协作自动焊接电感线圈,主机为电感抓取机器人,从机为焊接机器人(两台AIR6机器人)。
采用视觉准确识别产品位置,通过双机协作方式焊接电感线圈,并设有除烟尘设备,焊接安全可靠。
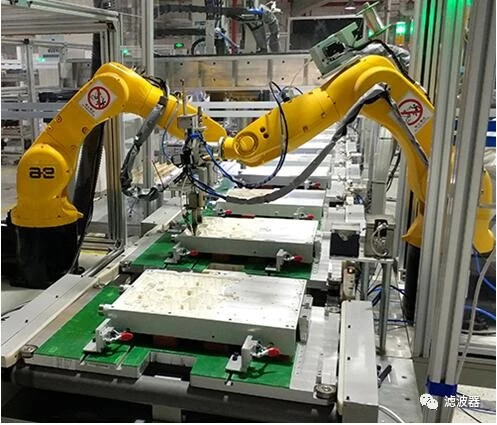
工艺简介:电感抓取机器人以视觉定位准确抓取电感到焊接位置;焊接机器人根据视觉定位信息准确焊接电感;焊接过程中产生的烟尘由烟尘净化装置处理。
■安装谐振杆
采用四轴直角坐标机器人完成谐振杆的安装及螺钉锁付。
末端兼容有抓取物料机构和螺钉锁付机构,结构紧凑,动作简单;采用吹气式螺钉供料机构,供料稳定,装配效率高。
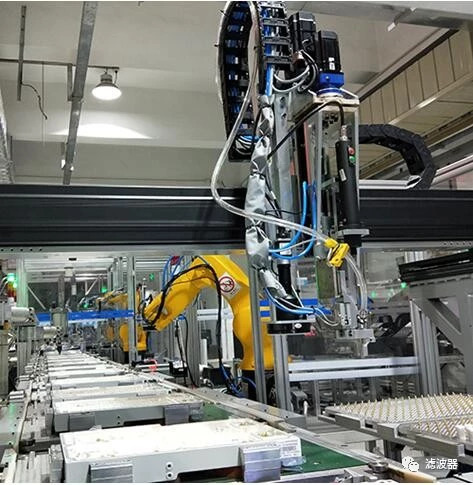
工艺简介:视觉标定滤波器工件坐标系;机器人自动抓取谐振杆;机器人自动装配并自动供螺钉进行锁付。
贴标扫码
采用AIR6机器人进行贴标以及扫码绑定上传工作。
采用吸盘吸取标签的方式,兼容性强。
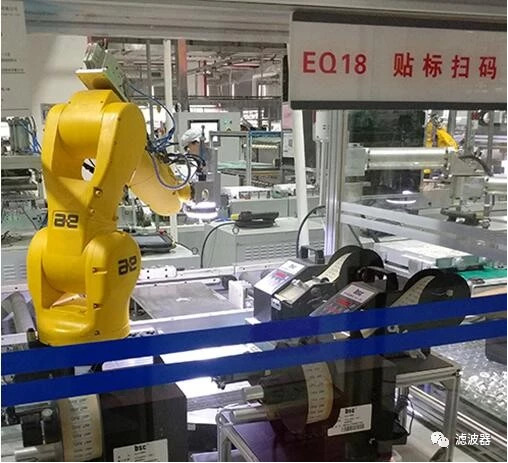
工艺简介:采用扫码器识别1个条形码以及4个二维码,并将相关信息通过机器人控制系统汇总到总控PLC,再上传smart系统,完成客户标签信息与PCB标签信息的绑定;视觉对滤波器腔体进行拍照,标定工件坐标系。机器人使用吸盘吸取标签,依次完成4个端口标签的贴标工作。
|